Non-destructive testing (NDT) is a wide group of analysis techniques used in science and technology industry to evaluate the properties of a material, component or system without causing damage.
Various national and international trade associations exist to promote the industry, knowledge about non-destructive testing, and to develop standard methods and training. These include the American Society for Nondestructive Testing, the Non-Destructive Testing Management Association, the International Committee for Non-Destructive Testing, the European Federation for Non-Destructive Testing and the British Institute of Non-Destructive Testing.
Non-destructive examination (NDE): the development and application of technical methods to examine materials and/or components in ways that do not impair future usefulness and serviceability in order to detect, locate, measure, interpret and evaluate flaws.
The manufacturing process is a combination of multiple processes used for transforming raw materials into finished products.
Types of manufacturing Systems:
1. The continuous system: Used to manufacture a large number of products by a continuous flow of materials through a series of operations under the same process control parameters such as nuts and bolts.
2. The batch system: used to manufacture products fixed numbers in batches such as shoes, clothes, etc.
3. The Fixed system: used to manufacture a product that cannot be moved between processes and work stations such as ships, airplanes, buildings, etc.
Destructive testing (destructive physical analysis, DPA):
It includes testing for specimen failure, for example, Tensile testing, Bend Test, Flexural Test, Impact Testing, fire-resistant. It gives a quantitative measure of material properties such as tensile stress, hardness, strength, toughness, etc. But the tested product loses its ability to use fullness.
Application of Destructive testing in Different manufacturing Systems:
1. In continuous systems large quantity of products are manufactured under the same process parameters hence it is not necessary to check or inspects all the manufactured pieces. Hence Sampling is carried out as per the manufacturing standard.
These samples undergo destructive testing and depending upon the test results of these samples, the whole lot is accepted or rejected. However it not necessary that if samples are found of required quantity each and every piece is of required quantity but this method gives maximum results with less loss of manufactured parts/pieces.
2. In batch systems, manufacturing control parameters change with every batch. Hence sampling is carried out in each batch and those samples undergo Destructive tests and depending upon the results of those samples whole batch is accepted or rejected.
3. In project Systems, there is only one big job which is needed to be inspected after each process. Here destructive testing after each process is not possible. Since destructive tests will make the product not useful for the indented purpose.
The issue with Destructive Testing
Before NDT was introduced in order to omit such scenario samples of the raw material, or batch samples of these products undergo destructive testing. Taking into consideration that if raw materials are of required specification the end product will be of the required quality. But Still, multiple accidents were reported of in-service failures of Equipment causing loss of property and human life.
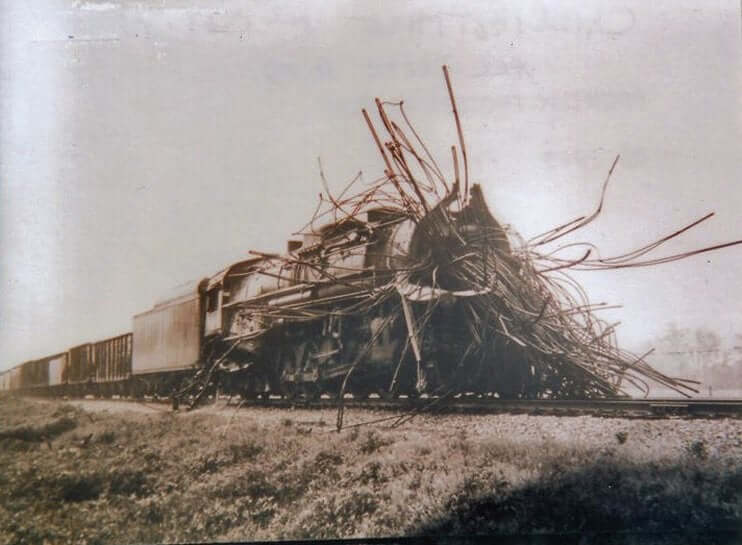
This made Non-destructive testing as much needed test method to eliminate such failures. Since non-destructive testing provides results without harming the product.
In today’s Industry, all most all critical products have a mandatory requirement for carrying out Non-destructive testing (NDT) in the manufacturing Code itself such as high-pressure valves, pressure vessels, oil pipelines, aircraft industries, automobile industry, railways and many more.
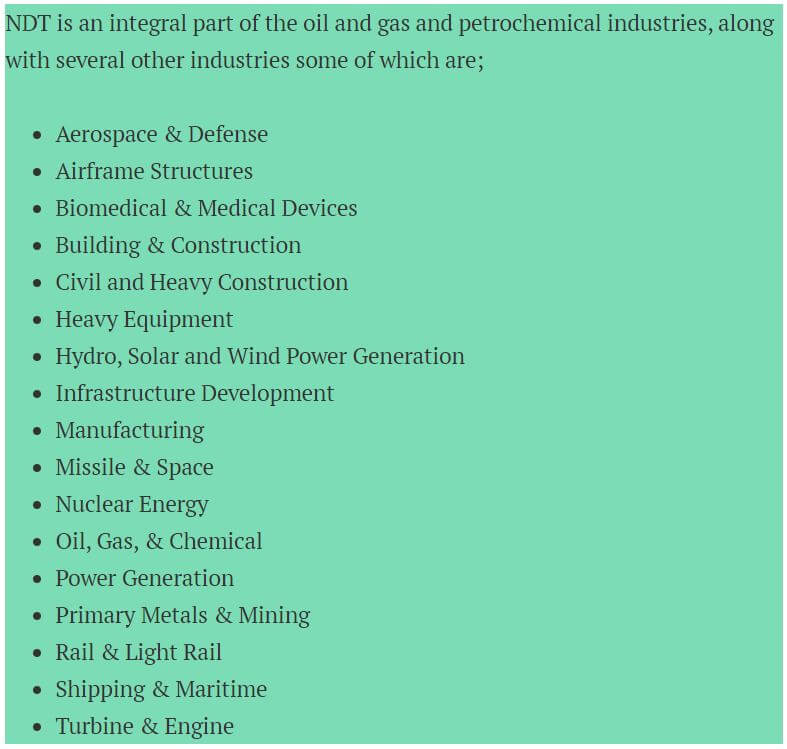
Benefits of Non-destructive testing (NDT):
- No damage to the original part
- No harm to the usefulness of Job/Product
- Can be carried out at multiple manufacturing stages (Raw material, semi-finished stage, or final stage)
- a comprehensive way to locate surface and internal flaws
- Potential Accident preventions
- reduce costs
- Increases product reliability
- Meet regulations and requirements
- Manage assets and resources
- Useful for in-service inspection
- Multiple applications depending upon manufacturing process and service conditions.
- Provide quality assurance
Conclusion
NDT is necessary whenever it is required to assure ourselves about the quality and reliability of crucial components without causing damage to the original part, whose in-service failure will cause loss of property and human life.
If you want to learn about the history of this crucial testing method read the article History of NDT which will give you a clear idea about how these methods came to use in today’s manufacturing industry.
Need for Non-destructive testing(NDT) FAQs:
Where is non-destructive testing used?
NDT is an integral part of the oil and gas and petrochemical industries, along with several other industries some of which are;
· Aerospace & Defense
· Airframe Structures
· Biomedical & Medical Devices
· Building & Construction
· Civil and Heavy Construction
· Heavy Equipment
· Hydro, Solar and Wind Power Generation
· Infrastructure Development
· Manufacturing
· Missile & Space
· Nuclear Energy
· Oil, Gas, & Chemical
· Power Generation
· Primary Metals & Mining
· Rail & Light Rail
· Shipping & Maritime
· Turbine & Engine
What is the difference between destructive and non-destructive testing?
DESTRUCTIVE TESTING (DESTRUCTIVE PHYSICAL ANALYSIS, DPA):
It includes testing for specimen failure, for example, Tensile testing, Bend Test, Flexural Test, Impact Testing, fire-resistant. It gives a quantitative measure of material properties such as tensile stress, hardness, strength, toughness, etc. But the tested product loses its ability to use fullness.
Where as
Non-destructive testing involves inspection of test object without cause any harm to the test object and without altering any properties of the test object.
References
- Wikipedia.org
- www.magnachek.com
It was interesting to learn the benefits of non-destructive testing. I like how you said that NDT can increase product reliability. I’d recommend finding an NDT service that has a lot of experience so you can trust them.
Thank you for explaining to us that non-destructive testing refers to the analysis done for manufacturing processes to evaluate the properties of a material component or system without damaging them. My brother recently started managing a welding company, and he is considering doing non-destructive testing on their products soon. I hope he finds a trustworthy professional to hire for this task soon and help give him good results.