UT Immersion testing techniques are mainly used in the laboratory and for large installations doing automatic ultrasonic testing. It has the advantage that uniform couplant conditions are obtained and longitudinal and transverse waves can be generated with the same probe simply by changing the incident beam angle. Immersion ultrasonic inspection is mainly utilized in shop applications as a method to very accurately locate, classify, and size defects in large plate, bar, or forged materials.
To learn more about ultrasonic testing read our blogs :
In immersion testing, a waterproof transducer is used at some distance from the test object, and the ultrasonic beam is transmitted into the material through a water path or column. The water distance appears on the display as a fairly wide space between the initial pulse and the front surface reflection because of the reduced velocity of sound in water.
The three basic techniques used in UT immersion testing are
- the immersion technique: here both the transducer and the test object are immersed in water.
- the bubbler technique or the squirter technique, where the sound beam is transmitted through a column of flowing water.
- the wheel transducer technique: here the transducer is mounted in the axle of a liquid-filled tire that rolls on the test surface.
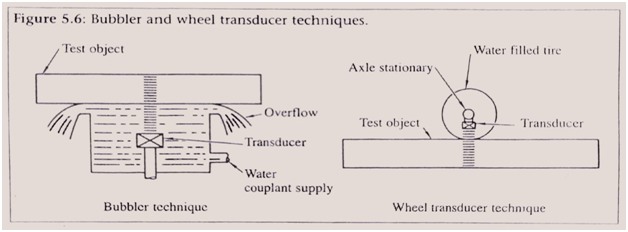
In all three of these techniques, a focused transducer that concentrates the sound beam to enhance the test.
In the immersion technique, both the probe and the test specimen are immersed in water. The ultrasonic beam is directed through the water into the test specimen, using either a normal beam technique for generating longitudinal waves or an angle beam technique for generating transverse waves.
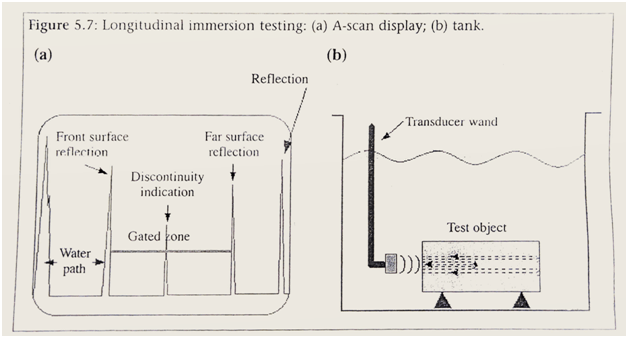
When the normal beam technique is being used the water path distance must always be longer than the distance ‘S’ in equation.

The graph of peaks using the immersion method is slightly different. Between the initial pulse and the back wall peaks, there will be an additional peak caused by the sound wave going from the water to the test material. This additional peak is called the front wall peak. The ultrasonic tester can be adjusted to ignore the initial pulse peak, so the first peak it will show is the front wall peak. Some energy is lost when the waves hit the test material, so the front wall peak is slightly lower than the peak of the initial pulse.
When the specimen is steel the water path must be longer than ¼ steel thickness otherwise 1st back wall echo overlaps the 2nd surface echo and defects near the back wall may not be seen.
Standard Immersion technique:
In UT immersion testing, both the transducer and the test object are immersed in water. The sound beam is directed through the water into the material, using either longitudinal waves or shear waves. in immersion testing, longitudinal wave transducers are used to accomplish both longitudinal and shear wave testing of the submerged test object. The entry angle of the ultrasonic wave is adjusted manually or by computer setting to produce the precise angle of refraction through the material that will result in a thorough test for anticipated discontinuity orientations.
The correct water path distance is particularly important when the test area shown on the A-scan display is gated for automatic signaling and recording operations. The water path distance is carefully set to clear the test area of unwanted signals, such as the second reflection from the front surface, which could cause misinterpretation.
Bubbler UT immersion Technique:
The bubbler technique is a variation of the UT immersion testing method. The bubbler is typically used with an automated system for high-speed scanning of plate, sheet, strip, rail, tubing, and other regularly shaped forms. The sound beam is projected into the material through a column of flowing water and is directed perpendicular to the test surface to produce longitudinal waves. It can also be adjusted at an angle to the surface to produce shear waves.
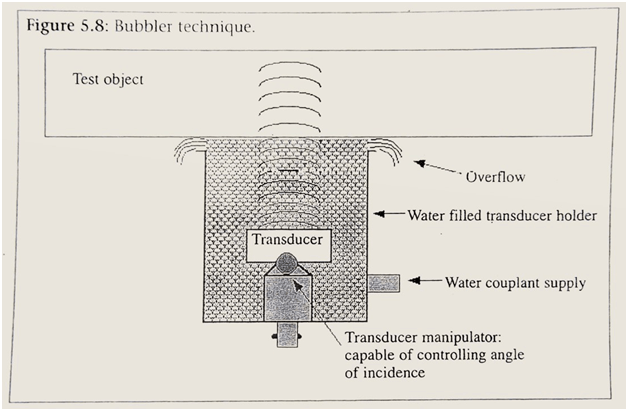
Wheel Transducers UT immersion Technique:
The wheel transducer technique is a variant of the UT immersion method in that the sound beam is projected through a water filled tire into the test object. The transducer, mounted in the wheel axle, is held in a fixed position while the wheel and the tire rotate freely. The wheel may be mounted on a mobile apparatus that runs across the material, or it may be mounted on a stationary fixture where the material is moved past it.
It is common practice within the railroad industry to use this ultrasonic testing technique. Wheel-mounted transducers are fixed to carriages that are mounted to high rail or rail-bound vehicles each of
the transducer wheels may contain several transducers and these transducers may be positioned to produce longitudinal and shear tests out of each wheel to detect internal discontinuities within the rails.
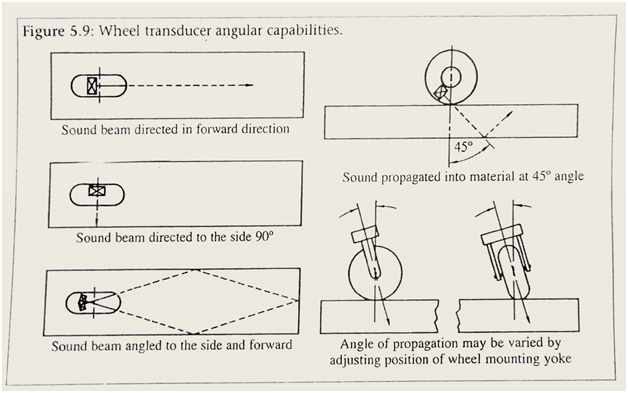
References :
PTP Ultrasonic Testing Classroom Training Book.