Magnetic particle testing is used to detect surface and shallow subsurface discontinuities such as cracks, laps, seams, cold shuts, and laminations in ferromagnetic materials (no other type of material) such as iron, nickel, cobalt, and some of their alloys. In principle, this method involves magnetizing an area to be examined and applying ferromagnetic particles (the examination’s medium) to the surface. Particle patterns form on the surface where the magnetic field is forced out of the part and over discontinuities to cause a leakage field (magnetic flux leakage) that attracts the particles. Particle patterns are usually characteristic of the type of discontinuity that is detected. There are multiple magnetization techniques for performing magnetic particle testing however whichever technique is used to produce the magnetic flux in the part, maximum sensitivity will be to linear discontinuities oriented perpendicular to the lines of flux. For optimum effectiveness in detecting all types of discontinuities, each area is to be examined at least twice, with the lines of flux during one examination being approximately perpendicular to the lines of flux during the other. In this article, we will learn about different techniques of magnetization to perform magnetic particle testing.
MAGNETIZATION TECHNIQUES
One or more of the following five magnetization techniques shall be used:
- (a) prod technique
- (b) longitudinal magnetization technique
- (c) circular magnetization technique
- (d) yoke technique
- (e) multidirectional magnetization technique
PROD TECHNIQUE
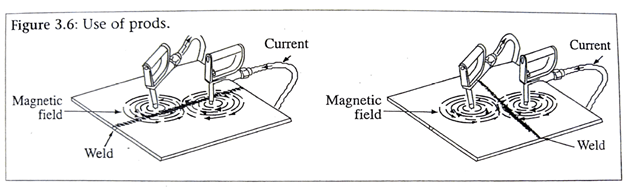
PC: ASNT MAGNETIC PARTICLE TESTING CLASSROOM TRAINING BOOK.
Magnetizing Procedure.
For the prod technique, magnetization is accomplished by portable prod type electrical contacts pressed against the surface in the area to be examined. To avoid arcing, a remote control switch, which may be built into the prod handles, shall be provided to permit the current to be applied after the prods have been properly positioned.
Magnetizing Current.
Direct or rectified magnetizing current shall be used. The current shall be 1 0 0 ( minimum ) amp / in . ( 4 amp/mm) to 125 (maximum) amp/in. (5 amp/mm) of prod spacing for sections 3/4 in. (19 mm) thick or greater. For sections, less than 3/4 in. (19 mm) thick, the current shall be90 amp/in. ( 3 . 6 amp/mm) to 110 amp/in. (4.4 amp/mm) of prod spacing.
Prod Spacing.
Prod spacing shall not exceed 8 in. (200 mm). Shorter spacing may be used to accommodate the geometric limitations of the area being examined or to increase the sensitivity, but prod spacing’s of less than 3 in. (75 mm) are usually not practical due to banding of the particles around the prods. The prod tips shall be kept clean and dressed. If the open-circuit voltage of the magnetizing current source is greater than 25 V, lead, steel, or aluminum (rather than copper) tipped prods are recommended to avoid copper deposits on the part being examined.
LONGITUDINAL MAGNETIZATION TECHNIQUE
Magnetizing Procedure.
For this technique, magnetization is accomplished by passing a current through a multi-turn fixed coil (or cables) that is wrapped around the part or section of the part to be examined. This produces a longitudinal magnetic field parallel to the axis of the coil. If a fixed, prewound coil is used, the part shall be placed near the side of the coil during the inspection. This is of special importance when the coil opening is more than 10 times the cross-sectional area of the part.
Magnetic Field Strength.
Direct or rectified current shall be used to magnetize parts examined by this technique. The required field strength shall be calculated based on the length L and the diameter D of the part in accordance with (a) and (b), or as established in (d) and (e), below. Long parts shall be examined in sections not to exceed 18 in. (450 mm), and 18 in. (450 mm) shall be used for the part L in calculating the required field strength. For noncylindrical parts, D shall be the maximum cross-sectional diagonal.
(a) Parts With L/D Ratios Equal to or Greater Than 4.
The magnetizing current shall be within 10% of the ampere-turns value determined as follows:
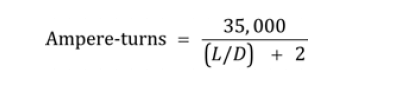
(b) Parts With L/D Ratios Less Than 4 but Not Less Than 2.
The magnetizing ampere-turns shall be within 10% of the ampere-turns value determined as follows:
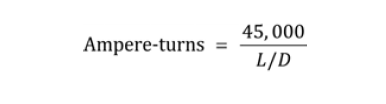
Parts With L/D Ratios Less Than 2. Coil magnetization technique cannot be used.
(d) If the area to be magnetized extends beyond 9 in. (225 mm) on either side of the coils center, field adequacy shall be demonstrated using a magnetic field indicator or artificial flaw shims per ASME BPVC SEC-V, ARTICLE 7 T-764.
(e) For large parts due to size and shape, the magnetizing current shall be 1200 ampere-turns to 4500 ampere-turns. The field adequacy shall be demonstrated using artificial flaw shims or a pie-shaped magnetic field indicator in accordance with ASME BPVC SEC-V, ARTICLE 7 T-764. A Hall-Effect probe gaussmeter shall not be used with encircling coil magnetization techniques.
Magnetizing Current.
The current required to obtain the necessary magnetizing field strength shall be determined by dividing the ampere-turns obtained in steps (a) or (b) by the number of turns in the coil as follows:

CIRCULAR MAGNETIZATION TECHNIQUE
Direct Contact Technique.
(a) Magnetizing Procedure.
For this technique, magnetization is accomplished by passing current through the part to be examined. This produces a circular magnetic field that is approximately perpendicular to the direction of current flow in the part.
(b) Magnetizing Current.
Direct or rectified (half-wave rectified or full-wave rectified) magnetizing current shall be used.
- The current shall be 300 amp/in. (12 A/mm) to 800 amp/in. (31 A/mm) of outer diameter.
- For parts with geometric shapes other than round, the greatest cross-sectional diagonal in a plane at right angles to the current flow shall be used in lieu of the outer diameter in (1) above.
- If the current levels required for (1) cannot be obtained, the maximum current obtainable shall be used and the field adequacy shall be demonstrated in accordance with ASME BPVC SEC-V, ARTICLE 7 T-764.
Central Conductor Technique.
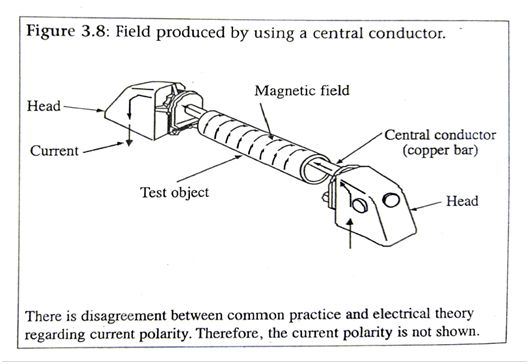
(a) Magnetizing Procedure.
For this technique, a central conductor is used to examine the internal surfaces of cylindrical or ring-shaped parts. The central conductor technique may also be used for examining the outside surfaces of these shapes. Where large-diameter cylinders are to be examined, the conductor shall be positioned close to the internal surface of the cylinder. When the conductor is not centered, the circumference of the cylinder shall be examined in increments. Field strength measurements in accordance with ASME BPVC SEC-V, ARTICLE 7 T-764 shall be used, to determine the extent of the arc that may be examined for each conductor position, or the rules in (c) below may be followed. Bars or cables passed through the bore of a cylinder, may be used to induce circular magnetization.
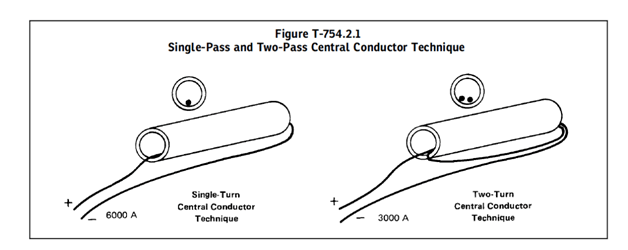
(b) Magnetizing Current.
The field strength required shall be equal to that determined in direct contact circular magnetization (b) for a single-turn central conductor. The magnetic field will increase in proportion to the number of times the central conductor cable passes through a hollow part. For example, if 6000 A are required to examine a part using a single pass central conductor, then 3000 A are required when 2 passes of the through-cable are used, and 1200 A are required if 5 passes are used (see Figure T-754.2.1). When the central conductor technique is used, magnetic field adequacy shall be verified using a magnetic particle field indicator in accordance with ASME BPVC SEC-V, ARTICLE 7 T-764.
(c) Offset Central Conductor.
When the conductor passing through the inside of the part is placed against an inside wall of the part, the current levels, as given in direct contact circular magnetization (b)(1) shall apply, except that the diameter used for current calculations shall be the sum of the diameter of the central conductor and twice the wall thickness. The distance along the part circumference (exterior) that is effectively magnetized shall be taken as four times the diameter of the central conductor, as illustrated in Figure T-754.2.2. The entire circumference shall be inspected by rotating the part on the conductor, allowing for approximately a 10% magnetic field overlap.
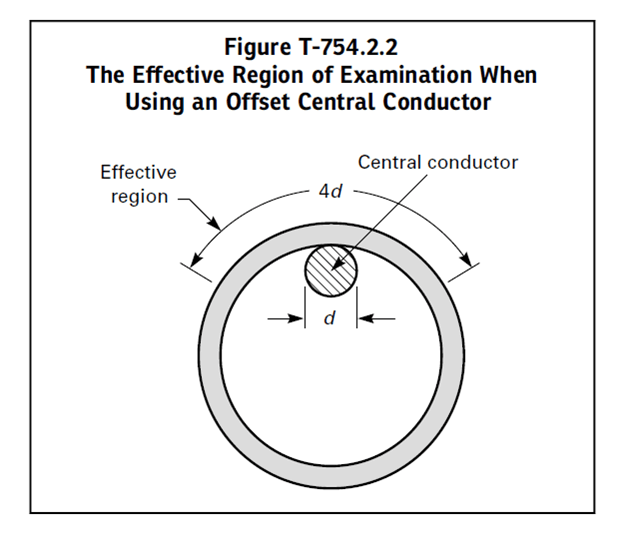
YOKE TECHNIQUE
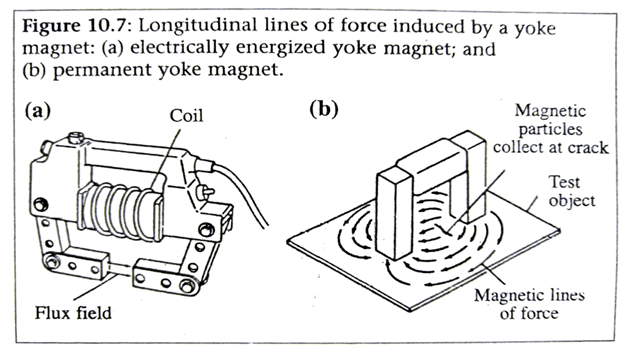
For this technique, alternating or direct current electromagnetic yokes, or permanent magnet yokes, shall be used. A longitudinal magnetic field can be induced in a test object or in a limited area of a test object by using a handheld yoke. A yoke is a U-shaped piece of soft magnetic material either solid or laminated around which is wound a coil carrying the magnetization current.
MULTIDIRECTIONAL MAGNETIZATION TECHNIQUE
Magnetizing Procedure.
For this technique, magnetization is accomplished by high amperage power packs operating as many as three circuits that are energized one at a time in rapid succession. The effect of these rapidly alternating magnetizing currents is to produce an overall magnetization of the part in multiple directions. Circular or longitudinal magnetic fields may be generated in any combination using the various techniques described in longitudinal and circular magnetization techniques mentioned above.
Magnetic Field Strength.
Only three phase, full-wave rectified current shall be used to magnetize the part. The adequacy of the magnetic field shall be demonstrated using artificial flaw shims or a pie-shaped magnetic particle field indicator in accordance with BPVC SEC-V, ARTICLE 7 T-764. A Hall-Effect probe gaussmeter shall not be used to measure field adequacy for the multidirectional magnetization technique. An adequate field shall be obtained in at least two nearly perpendicular directions, and the field intensities shall be balanced so that a strong field in one direction does not overwhelm the field in the other direction. For areas where adequate field strengths cannot be demonstrated, additional magnetic particle techniques shall be used to obtain the required two-directional coverage.
REFERENCES:
- ASNT MAGNETIC PARTICLE TESTING CLASSROOM TRAINING BOOK.
- ASME BPVC SEC-V ARTICLE 7